Plastic Prototype Manufacturing: Revolutionizing Business Development
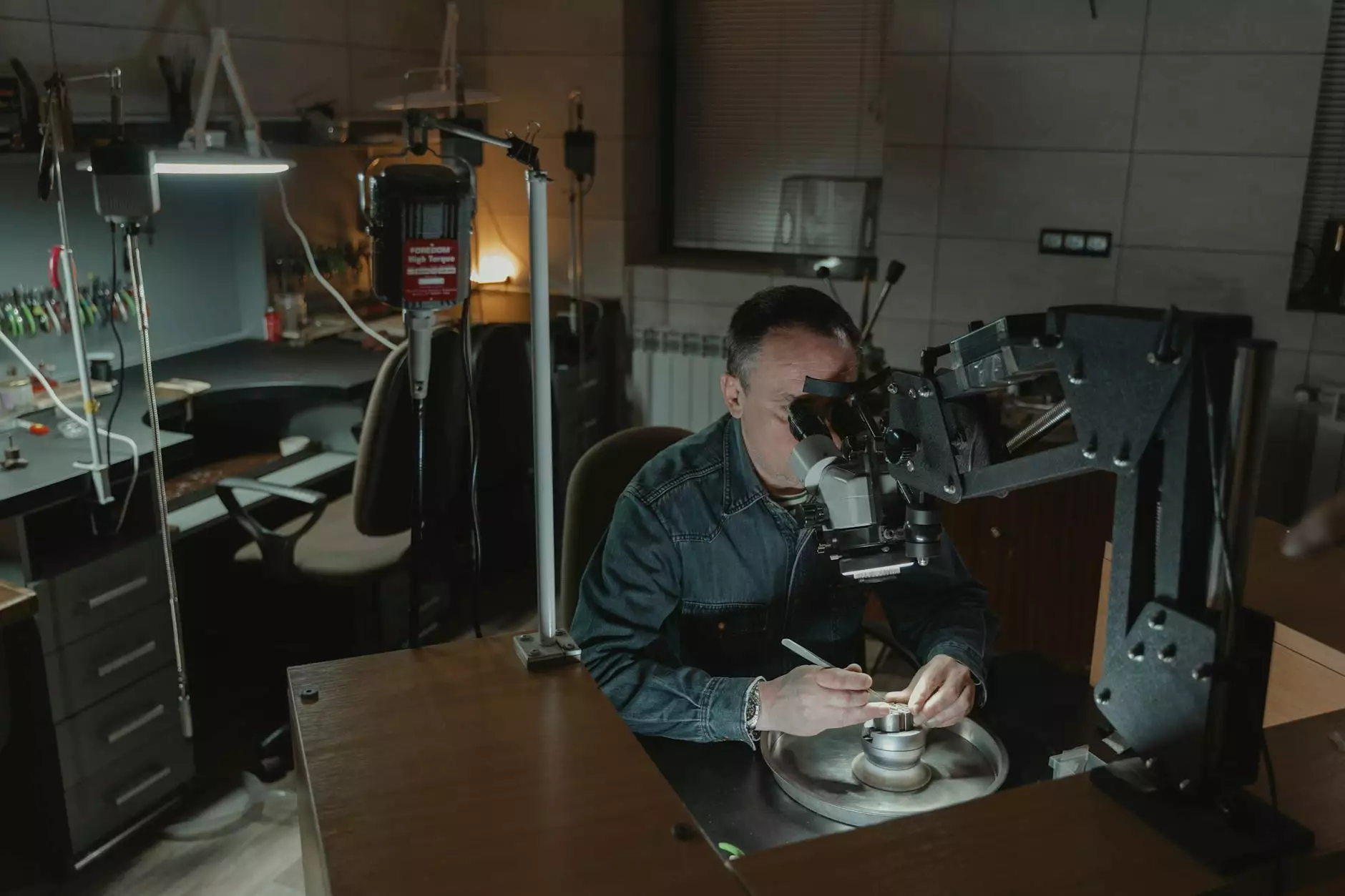
In today's competitive landscape, businesses are constantly seeking ways to innovate and improve their product offerings. One of the most significant advancements in this area is plastic prototype manufacturing. This process not only allows for the rapid creation of product prototypes but also paves the way for efficient product development and market responsiveness. This article delves deep into the benefits of prototype manufacturing, its processes, and how it can fuel the growth of businesses across various industries.
Understanding Plastic Prototype Manufacturing
Plastic prototype manufacturing refers to the process of creating a physical model of a product using plastic materials. This can include various techniques such as 3D printing, injection molding, CNC machining, and more. The primary goal is to produce a prototype that accurately represents the final product, allowing for testing, assessment, and refinement before full-scale production.
Key Benefits of Plastic Prototype Manufacturing
- Accelerated Product Development: By leveraging prototype manufacturing, businesses can significantly reduce lead times. Designers can quickly create and test iterations of their products, leading to faster commercialization.
- Cost Efficiency: Producing prototypes in bulk can be expensive. However, with the right manufacturing processes, companies can minimize costs while still achieving high-quality results.
- Enhanced Design Validation: Prototypes allow teams to validate designs practically. This hands-on experience helps identify potential design flaws before moving into mass production.
- Improved Communication: Prototypes serve as tangible communication tools that facilitate discussions between designers, engineers, and stakeholders. This transparency leads to better decision-making.
- Market Testing: Developing a prototype enables businesses to conduct market testing early in the product lifecycle, gathering valuable feedback to refine offerings before launching.
The Process of Plastic Prototype Manufacturing
To fully appreciate the advantages of plastic prototype manufacturing, it's essential to understand the various methods employed in the process. Each method offers unique benefits depending on the specific requirements of the project.
1. 3D Printing
3D printing, also known as additive manufacturing, involves creating three-dimensional objects layer by layer using a computer-aided design (CAD) file. It is particularly beneficial for producing complex geometries and can be executed quickly.
Advantages of 3D Printing:
- Rapid prototyping capabilities allow for quick iterations.
- Lower production costs for small quantities.
- The flexibility of designs that can be easily modified.
2. Injection Molding
Injection molding is a process where molten plastic is injected into a mold to create a certain shape. While it requires a significant initial investment for the mold creation, it is incredibly cost-effective for larger production runs.
Advantages of Injection Molding:
- High precision and repeatability in the produced items.
- Cost efficiency in larger production volumes.
- Ability to use a variety of materials and plastics.
3. CNC Machining
CNC machining involves removing material from a solid block to create the desired shape. This method is particularly useful for creating durable prototypes, especially if mechanical strength is required.
Advantages of CNC Machining:
- Wide range of materials can be used, including metals.
- High precision and quality of the final product.
- Very effective for low-volume production runs.
Applications of Plastic Prototypes Across Industries
Plastic prototype manufacturing plays a pivotal role in multiple sectors, helping businesses optimize their design and testing processes. Here are some prominent industries that benefit significantly from this innovation.
1. Automotive
In the automotive industry, rapid prototyping is critical for designing and testing new components such as dashboards, panels, and external coverings. By utilizing plastic prototype manufacturing, manufacturers can swiftly iterate designs, ensuring both aesthetic appeal and functional performance.
2. Consumer Electronics
With the fast-paced development cycles in consumer electronics, companies rely on prototyping to refine designs for products such as smartphones, laptops, and wearables. Prototypes allow engineers to address usability, ergonomics, and design issues early in the development phase.
3. Healthcare
The healthcare industry uses prototypes extensively for developing medical devices and equipment. Prototyping facilitates compliance with regulatory standards while enabling engineers to create user-friendly and effective healthcare solutions.
4. Toys and Games
The toy industry benefits tremendously from the quick turnaround of prototypes. Manufacturers can test concepts with children, gathering feedback for enhancements before full-scale production, thereby ensuring market success.
Choosing the Right Prototype Manufacturing Partner
Selecting the right partner for plastic prototype manufacturing is crucial for success. Here are some factors to consider:
1. Expertise and Experience
Evaluate the company's experience in handling projects similar to yours. A provider like deepmould.net with vast experience in metal fabrication and prototyping can bring valuable insights to your project.
2. Technology Capabilities
Ensure the manufacturer utilizes advanced technologies that align with your production needs, whether it’s 3D printing, injection molding, or CNC machining.
3. Quality Assurance
Inquire about their quality control processes. The ability to deliver high-quality prototypes is essential for accurate testing and evaluation.
4. Communication and Support
Choose a partner who values communication and provides support through every stage of development. This will ensure you remain informed and involved in the process.
The Future of Plastic Prototype Manufacturing
The future of plastic prototype manufacturing is incredibly promising, driven by technological advancements and growing demand across various industries. Innovations such as integrated artificial intelligence in design software, bio-based plastics, and sophisticated hybrid manufacturing processes are already setting the stage for the next wave of prototyping.
Emerging Trends:
- Sustainability: As environmental concerns mount, businesses are seeking sustainable materials for prototyping, pushing toward biodegradable plastics and recycled materials.
- AI and Automation: Artificial intelligence will play a role in optimizing designs and predicting manufacturing outcomes, improving efficiency and effectiveness.
- Digital Twins: This technology allows for the creation of virtual replicas of physical objects, aiding in testing and validation processes before any physical prototype is made.
Conclusion
In conclusion, plastic prototype manufacturing represents a cornerstone of modern product development. By enabling rapid iteration, enhancing communication, and validating designs, it plays an essential role in helping businesses innovate and stay competitive. As industries continue to evolve, the importance of effective prototyping will only grow stronger, ensuring that companies can bring their best ideas to market with speed and efficiency. For businesses poised to leverage this transformative process, partnering with a knowledgeable manufacturer like deepmould.net is a strategic move toward achieving sustained success and innovation.