Prototyping Rubber Bellows: Unlocking Innovation for Businesses
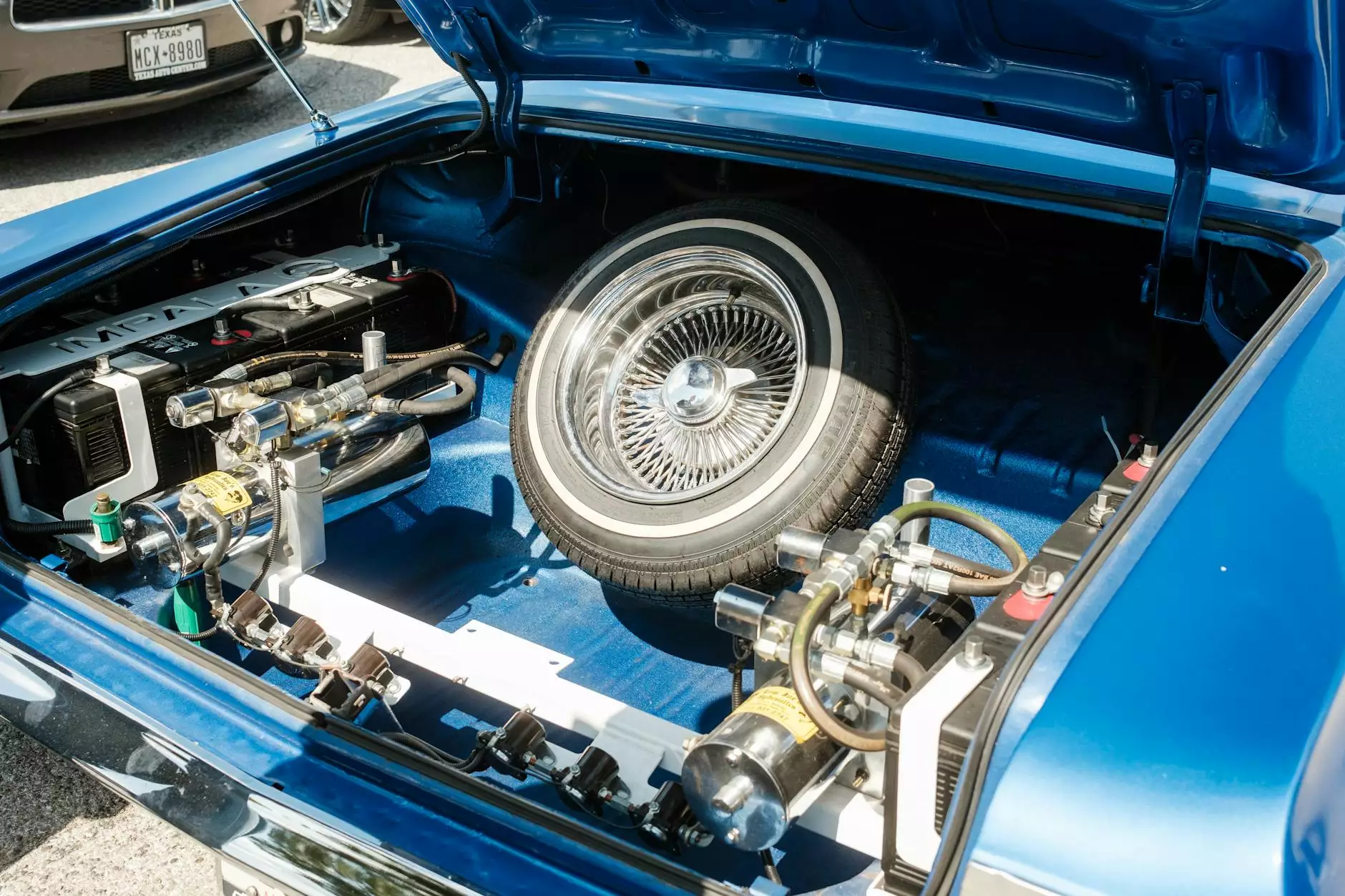
Prototyping rubber bellows has become a pivotal aspect of modern manufacturing, driving innovation and efficiency across various industries.
Understanding Rubber Bellows
Rubber bellows are flexible, expandable components designed to accommodate movement, vibration, and environmental factors while protecting internal parts from contamination. Their design allows them to function effectively in a variety of applications, enhancing durability and reliability.
What Are Rubber Bellows Made From?
Typically, rubber bellows are manufactured from materials such as:
- Natural Rubber: Known for its elasticity and strength, ideal for numerous applications.
- Synthetic Rubber: Includes types like EPDM, Neoprene, and Silicone, offering enhanced temperature and chemical resistance.
- Thermoplastic Elastomers (TPE): Provide excellent clarity, flexibility, and strength, suitable for various industries.
The Role of Prototyping in Rubber Bellow Manufacturing
Prototyping rubber bellows is an essential step in their manufacturing process. It allows engineers to test and refine designs before mass production. By creating a prototype, businesses can evaluate factors such as:
- Performance: Testing how the bellow behaves under real-world conditions.
- Fit and Compatibility: Ensuring the prototype fits seamlessly with other components.
- Ductility and Flexibility: Assessing the material's ability to withstand stress and movement.
Benefits of Prototyping Rubber Bellows
The advantages of prototyping rubber bellows in the design and manufacturing phase are manifold:
- Cost Efficiency: Identifying design flaws in the prototype phase can save significant costs in the long run.
- Customizability: Prototyping allows for adjustments based on specific needs and requirements, enhancing product functionality.
- Faster Time-to-Market: Rapid prototyping techniques can expedite the development process significantly.
- Higher Quality Products: Rigorous testing during prototyping ensures that only the best designs are put into production.
Applications of Rubber Bellows
Rubber bellows find usage in diverse sectors, including:
- Automotive Industry: Used in suspension systems, air intake systems, and steering racks.
- Electronics: Protect sensitive components from dust and moisture.
- Industrial Machinery: Utilized in conveyor systems and packaging equipment to maintain operational integrity.
- Aerospace: Essential in systems requiring high flexibility while maintaining a robust seal against environmental pressures.
Choosing the Right Provider for Prototyping Rubber Bellows
When sourcing prototyping rubber bellows, selecting the right partner is crucial for ensuring quality and performance. Here are key factors to consider:
- Experience: Look for a provider with substantial experience in rubber bellow prototyping and manufacturing.
- Technology: Ensure they use advanced technologies such as 3D printing to expedite and enhance the prototyping process.
- Material Knowledge: A good supplier should have extensive knowledge of various rubber materials and their applications.
- Customization Capabilities: The ability to customize designs based on specific requirements is essential for effective prototyping.
- Customer Support: Good communication and support can facilitate smoother prototyping processes.
3D Printing and Prototyping Rubber Bellows
With the advent of 3D printing technology, prototyping rubber bellows has become even more efficient and accessible. Here are several ways 3D printing enhances this process:
- Speed: The ability to quickly produce prototypes allows for rapid iteration and design improvement.
- Precision: 3D printing provides highly accurate dimensions, ensuring that the final product meets stringent specifications.
- Complex Designs: It enables the creation of intricate designs that would be difficult or impossible to achieve with traditional methods.
- Cost Savings: Reducing material waste and manufacturing time can lead to significant cost savings in the prototyping phase.
Future Trends in Prototyping Rubber Bellows
As industries continue to evolve, so do the methodologies applied to prototyping rubber bellows. Here are some emerging trends worth noting:
- Integration with IoT: Smart rubber bellows with integrated sensors that monitor performance and wear are becoming common.
- Sustainability: Increasing use of eco-friendly materials and manufacturing processes to produce rubber bellows.
- Collaboration with AI: AI-driven design tools are being used to optimize rubber bellow designs for performance and material efficiency.
- Advancements in Materials: Development of new rubber compounds for enhanced performance in extreme conditions.
Conclusion
In conclusion, prototyping rubber bellows represents a critical area of innovation in manufacturing. By embracing modern prototyping methods, including 3D printing, businesses can achieve significant advancements in quality, efficiency, and overall product satisfaction. At O'Victor Group, we are committed to providing high-end solutions for your prototyping needs, ensuring that you remain at the forefront of your industry.
Whether you're in the automotive, aerospace, or industrial sector, leveraging the power of flexible and durable rubber bellows will continue to drive your success into the future. Don’t hesitate to explore our range of services under Accessories and 3D Printing categories tailored to meet your unique business needs. Together, let’s build the future of innovation.