Understanding Prototype Molds: The Path to Quality Manufacturing
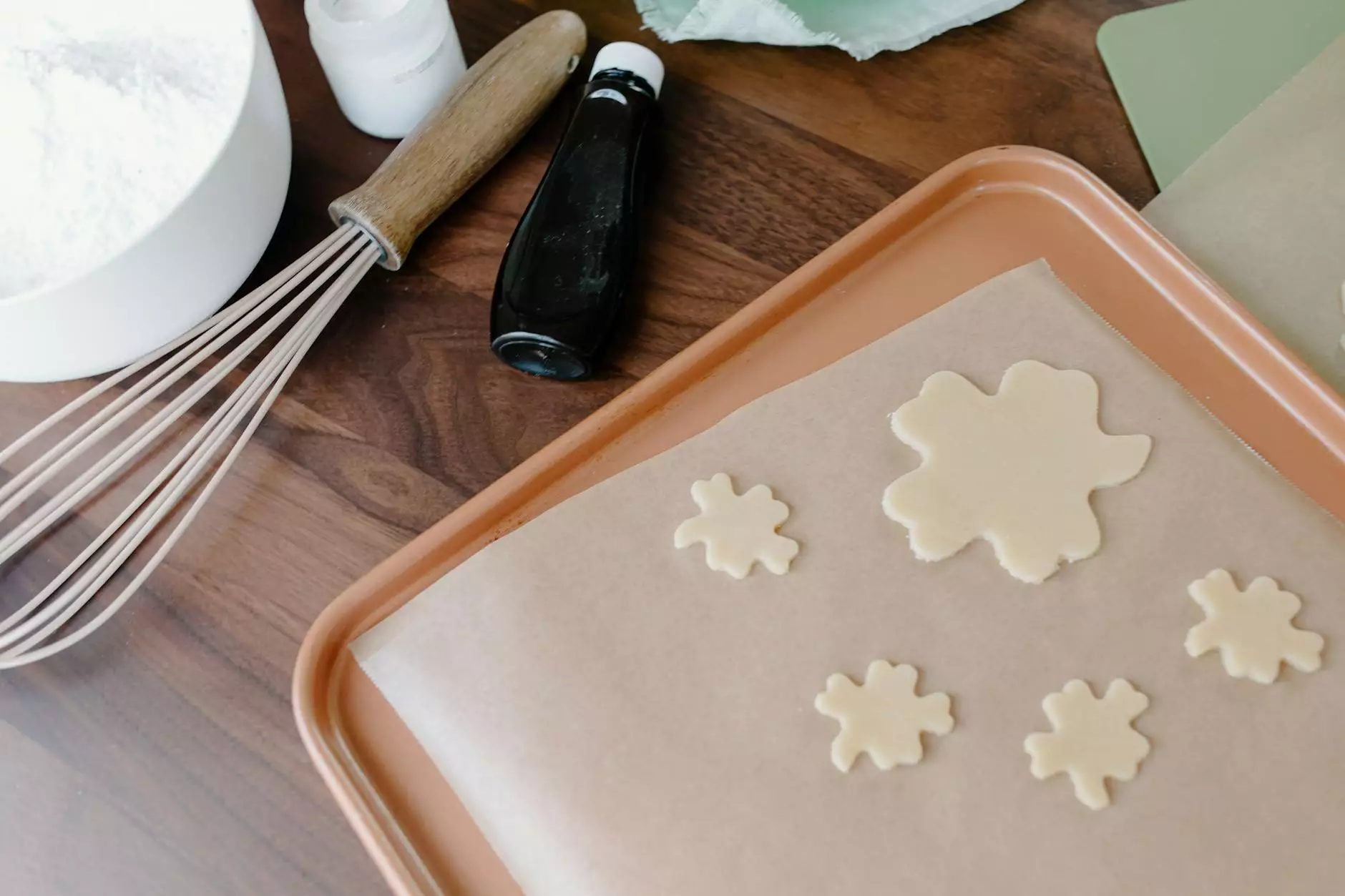
In the world of metal fabrication, the significance of prototype molds cannot be overstated. These molds are intricately designed tools that help businesses create precise and accurate prototypes of their products. This article delves deep into the intricacies of prototype molds, exploring their importance, the processes involved in their creation, and their impact on the manufacturing landscape.
The Importance of Prototype Molds in Metal Fabrication
Every innovative product starts with an idea. However, turning that idea into a tangible item involves several critical steps, and one of the most essential of these is the development of a prototype mold. A prototype mold serves as a preliminary model from which products can be developed, tested, and refined. Here are some notable reasons why prototype molds are vital in metal fabrication:
- Precision: Prototype molds are engineered to ensure that the resulting products have optimal precision, making them essential for industries that rely on exact specifications.
- Cost-Effective Testing: With a prototype mold, companies can test designs without the substantial investment of full-scale production, thus saving money and resources.
- Iteration: The ability to create multiple prototypes allows for quick iterations based on feedback, leading to better final products.
- Quality Assurance: Prototype molds help identify design flaws early in the development process, contributing to higher quality outcomes.
Types of Prototype Molds
Understanding the various types of prototype molds can enhance your approach to the design and manufacturing processes. Below are some common types of prototype molds used across different industries:
1. Soft Tooling
Soft tooling involves the use of materials that are easier to manipulate, such as silicone or aluminum. These types of molds are cost-effective and well-suited for low-volume production, making them ideal for testing concepts.
2. Hard Tooling
Hard tooling utilizes more durable materials such as steel. While more expensive, these molds offer higher longevity and are suitable for larger production runs. They are critical for products that require strict adherence to specifications and quality standards.
3. 3D Printed Molds
With advancements in technology, creating 3D printed molds has become feasible. These molds provide quick turnarounds and the flexibility to modify designs rapidly, making them popular for rapid prototyping.
The Process of Creating Prototype Molds
Creating a prototype mold is an intricate process that involves several steps, each of which is paramount to achieving the desired results. Below is a detailed overview of the stages involved in prototype mold creation:
1. Design Engineering
The first step in the process is thorough design engineering. Engineers analyze the product’s specifications, functions, and requirements to develop a mold design that accurately represents the product.
2. Material Selection
Choosing the appropriate materials for the prototype mold is crucial. This decision impacts the mold's durability, precision, and overall performance. Typical materials include:
- Steel
- Aluminum
- Silicone
- Plastic
3. Machining the Mold
Once the design and materials are finalized, machining begins. This process involves cutting, shaping, and finishing the mold components using advanced CNC machines, which ensure high levels of accuracy.
4. Assembly
After machining, the individual components are assembled to form the prototype mold. Inspectors closely evaluate the assembly to guarantee that all parts fit seamlessly, which is vital for producing high-quality prototypes.
5. Testing and Quality Control
Before the prototype mold is used for production, it undergoes rigorous testing. Engineers produce test parts to assess the mold’s performance, making adjustments as needed to improve outcomes.
Benefits of Using Prototype Molds
The advantages of utilizing prototype molds in your manufacturing processes are substantial. Here are some key benefits:
- Enhanced Development Time: Prototype molds speed up the product development cycle, allowing for faster time-to-market.
- Improved Product Quality: The iterative nature of prototype testing leads to superior product quality, enhancing customer satisfaction.
- Risk Mitigation: Identifying design flaws early reduces the risk of expensive mistakes in full-scale production.
- Market Adaptability: Companies can quickly pivot designs based on market feedback, maintaining relevance and competitiveness.
Challenges in Prototype Mold Creation
While the advantages are clear, challenges in creating and using prototype molds also exist. Addressing these challenges effectively can lead to successful outcomes:
1. Cost Constraints
Developing high-quality prototype molds can involve significant investment, particularly in hard tooling. Companies must balance costs with the need for precision and quality.
2. Time Consumption
Creating prototype molds and conducting thorough testing can be time-consuming. Efficient processes and technologies are necessary to minimize delays.
The Future of Prototype Molds in Manufacturing
As technology continues to advance, the future of prototype molds is evolving. Emerging trends to watch include:
- Increased Automation: The integration of automation technologies in mold manufacturing processes is expected to enhance efficiency and accuracy.
- Sustainability: Eco-friendly materials and processes will likely gain traction, aligning with global sustainability goals.
- Advanced Materials: The development of new materials that offer enhanced properties will broaden the capabilities of prototype molds.
Conclusion
In conclusion, the role of prototype molds in the realm of metal fabrication is indispensable. They provide significant advantages in product development, enhance quality assurance, and facilitate faster time-to-market strategies. By understanding the types, processes, and benefits associated with prototype molds, businesses can leverage their capabilities for enhanced innovation and competitiveness.
At Deep Mould, we are committed to providing exceptional prototype mold solutions tailored to your needs. Stay ahead of the competition by integrating advanced mold technologies into your manufacturing processes today!