Unlocking the Power of Die Casting Dies in Metal Fabrication
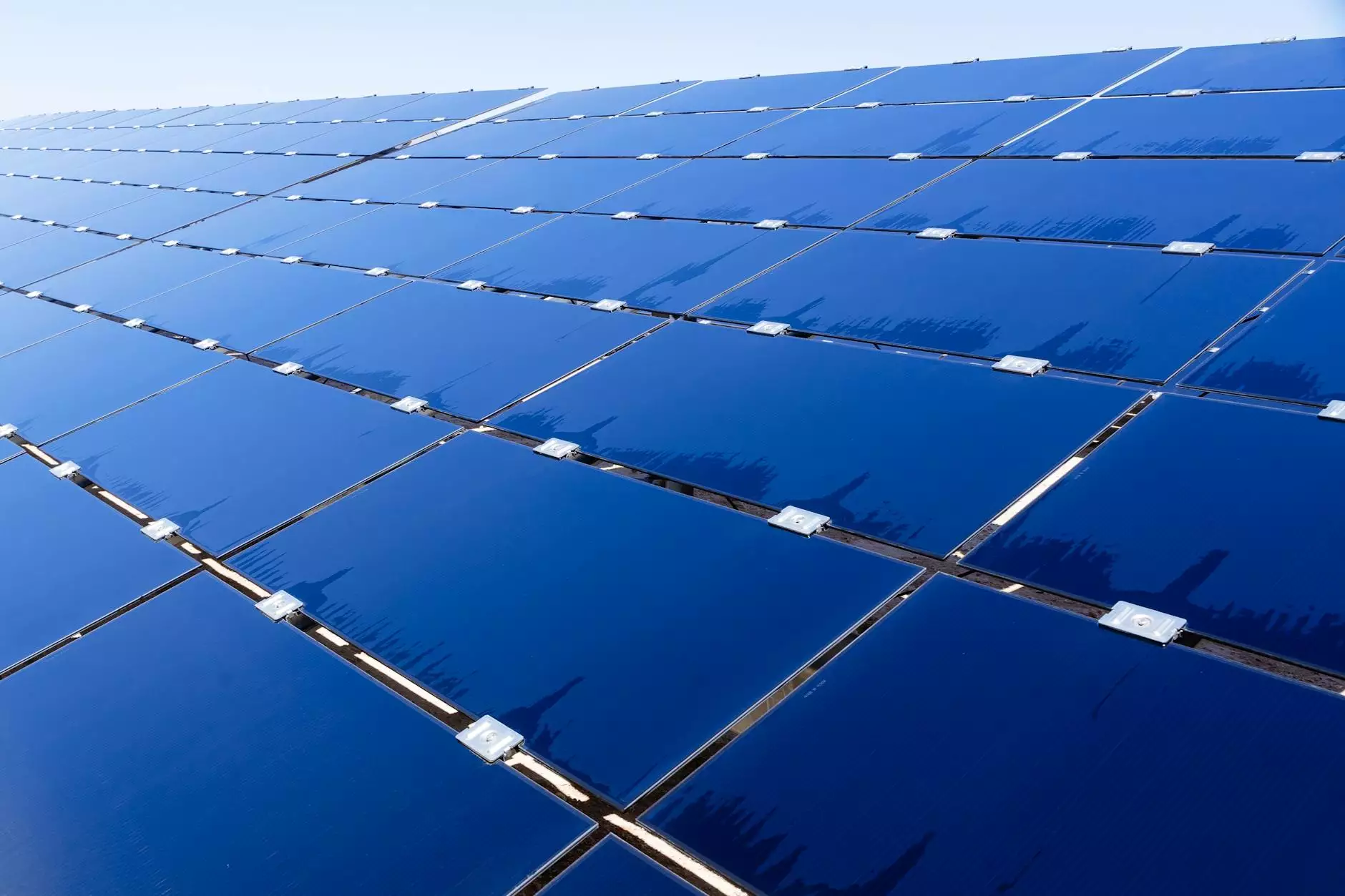
The world of manufacturing is replete with advanced technologies and innovative methods, one of which is die casting. Central to the success of this process are die casting dies, which play a crucial role in shaping metal components for various industries. In this article, we will explore the significance of die casting dies, their applications, and the factors you should consider when choosing the right ones for your business.
The Essentials of Die Casting Dies
To fully appreciate the capabilities of die casting dies, it's important to understand their fundamental components and processes. Die casting is a manufacturing process that involves forcing molten metal into a mold cavity. The mold, created from die casting dies, is crucial in defining the characteristics of the finished product.
What are Die Casting Dies?
Die casting dies are precision molds crafted to form molten metal into specific shapes during the die casting process. These dies are typically made from high-strength steel or other durable materials capable of withstanding high pressure and temperature. They are designed to withstand wear and tear, ensuring longevity and consistency in production.
Types of Die Casting Dies
- Hot Chamber Dies: Best suited for metals with low melting points (like zinc), hot chamber dies involve dipping the molten metal directly into the chamber during the process.
- Cold Chamber Dies: For metals with high melting points (such as aluminum), cold chamber dies require the molten metal to be poured into the chamber prior to being injected.
Benefits of Using Die Casting Dies
Leveraging die casting dies offers a myriad of advantages to manufacturers. Understanding these benefits will help you appreciate their role in your production process.
1. Enhanced Precision and Detail
One of the standout features of die casting is its ability to produce intricate shapes with remarkable precision. Die casting dies allow for highly detailed designs, enabling manufacturers to create complex components that meet specific tolerances. This precision is critical in industries like aerospace, automotive, and electronics, where component integrity is paramount.
2. Improved Production Efficiency
Die casting dies facilitate a rapid production process, significantly reducing cycle times when compared to traditional manufacturing methods. The quick cooling of the metal after it is injected into the mold promotes faster output rates. In a competitive market, this efficiency translates to enhanced productivity and cost savings.
3. Material Utilization and Waste Reduction
Within the context of metal fabrication, effective material utilization is essential. The die casting process minimizes scrap material, reducing waste and operational costs. This efficiency not only contributes to a more sustainable manufacturing process but also maximizes the return on investment for die casting dies.
4. Durable and Strong Components
Components produced through die casting are known for their strength and durability. The die casting dies create parts that exhibit superior mechanical properties, making them suitable for heavy-duty applications. This strength is particularly beneficial in industries that demand high-performance materials.
Applications of Die Casting Dies
Die casting dies find extensive applications across numerous industries. Their versatility makes them invaluable in the modern manufacturing landscape.
Aerospace Industry
The aerospace sector relies on die casting for producing lightweight yet robust components. Die casting dies are employed to create intricate parts that contribute to improved fuel efficiency and overall performance of aircraft.
Automotive Industry
In the automotive industry, die casting is integral to producing engine blocks, transmission cases, and other critical components. Using die casting dies streamlines production and enhances the reliability of automotive parts.
Consumer Electronics
Consumer electronics manufacturers utilize die casting dies to craft precise housings and structural components for devices ranging from smartphones to laptops. The aesthetic appeal and durability provided by die-cast parts cater to consumer demands for high-quality products.
Factors to Consider When Choosing Die Casting Dies
Selecting the right die casting dies is crucial for optimizing your manufacturing process. Here are some essential considerations to keep in mind:
1. Material Choice
Choosing the appropriate material for your dies is fundamental. Dies can be fabricated from various types of steel, including tool steel and alloy steel, depending on the specific requirements for durability, hardness, and heat resistance.
2. Complexity of Design
Assess the complexity of the components you intend to manufacture. More intricate designs demand highly skilled craftsmanship in the die casting dies to ensure precision and conformity to specifications.
3. Budget
While investing in high-quality die casting dies is essential, it's equally important to work within budgetary constraints. High-quality dies offer longevity and efficiency, reducing the cost in the long run.
4. Production Volume
Anticipating the volume of production will influence your decision on die casting dies. High-volume manufacturing may justify more significant initial investments in durable dies as they provide greater returns over time.
Maintenance and Care for Die Casting Dies
The longevity of die casting dies can be significantly impacted by proper maintenance. Regular cleaning, inspection, and lubrication are essential practices to prolong the life of the dies and ensure they function optimally.
1. Routine Cleaning
After each production run, the die should be thoroughly cleaned to remove any residue or buildup of metal particles. Keeping the die free from contaminants is vital for maintaining precision in future production cycles.
2. Inspection for Wear and Tear
Regularly inspect the die for signs of wear, cracking, or damage. Early detection of issues can prevent costly production delays and prolong the lifecycle of the dies.
3. Lubrication
Applying the correct lubrication to movable parts of the die aids in reducing friction and wear during the die casting process. Appropriate lubrication can minimize issues with sticking and improve the quality of the cast parts.
Conclusion
In conclusion, die casting dies are an integral component of the die casting process, providing manufacturers with the ability to produce precise, strong, and intricate components across various industries. By understanding their functionality, choosing the right dies, and maintaining them effectively, businesses can enhance their metal fabrication capabilities and achieve greater operational efficiency.
With the ongoing advancements in technology and materials, the future of die casting holds promising potential. By leveraging the power of die casting dies, companies like DeepMould.net can not only meet the demands of the current market but also set a benchmark for quality and innovation in the manufacturing landscape.