Micro Precision Injection Molding: The Future of Manufacturing
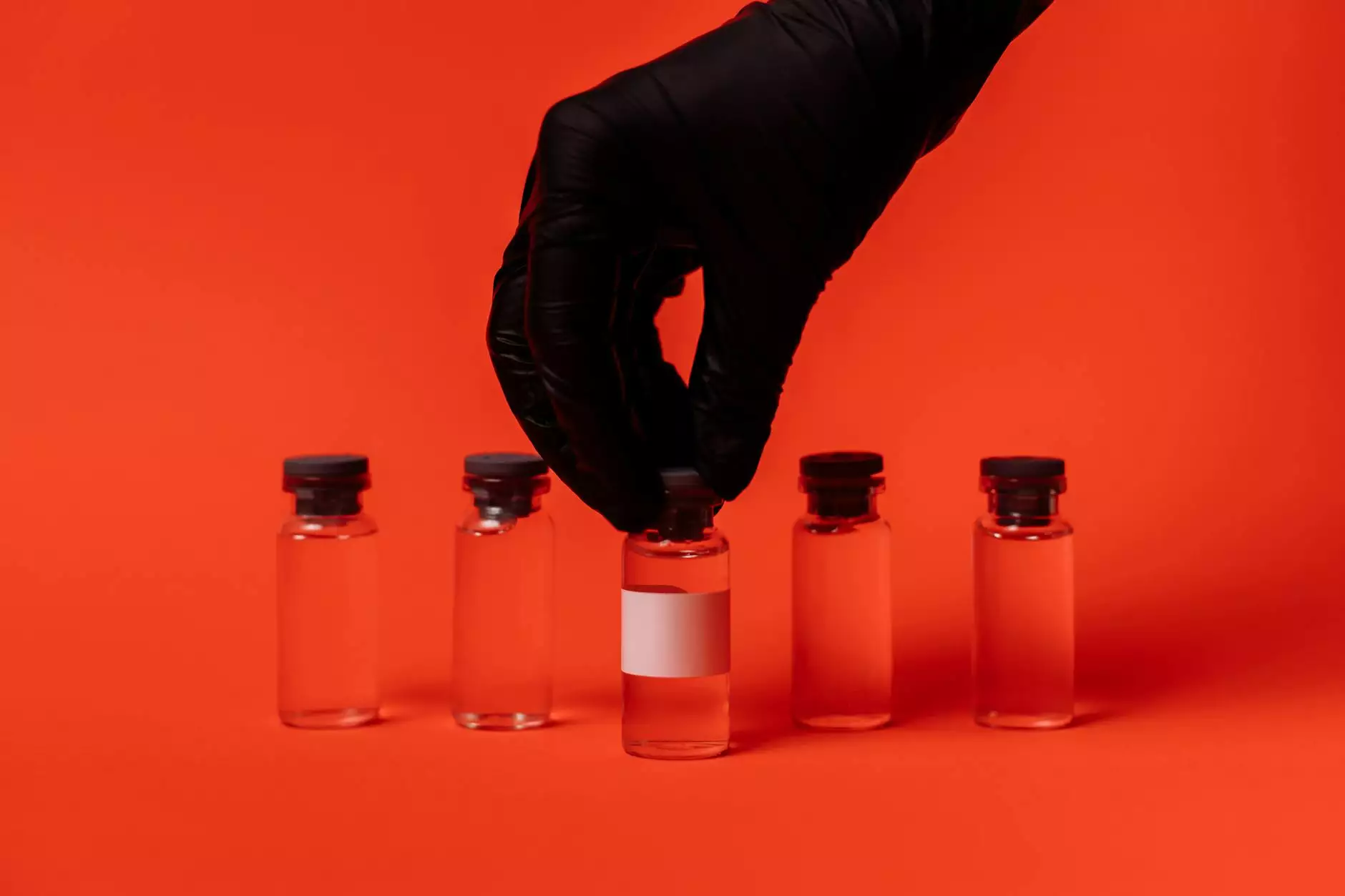
In the ever-evolving world of manufacturing, micro precision injection molding stands out as a groundbreaking technology that is redefining production processes across multiple industries. This specialized technique is pivotal in creating intricate components at an unprecedented scale, meeting the demands of an increasingly precise market. From medical devices to electronics, the applications of micro precision injection molding are vast and varied, offering high-quality solutions for complex projects.
Understanding Micro Precision Injection Molding
Micro precision injection molding is a manufacturing process where plastic or other materials are injected into molds to create small, highly detailed parts with exceptional accuracy. Unlike traditional injection molding, which produces larger components, this technique focuses on creating products that are often less than 1 gram in weight and can feature complex geometries.
Key Characteristics
- High Precision: Tolerances can be as tight as ±0.01 mm.
- Efficient Production: Capable of high-volume output with minimal waste.
- Complex Geometries: Ability to produce parts with intricate designs.
- Material Versatility: Works with a variety of thermoplastics and thermosetting materials.
The Advantages of Micro Precision Injection Molding
The advantages of adopting micro precision injection molding in manufacturing processes are manifold. Below are some of the primary benefits:
1. Increased Efficiency
The precision of this molding technique allows manufacturers to create parts with less material waste and energy consumption, leading to a more sustainable production process. High-speed injection molding machines can produce thousands of parts in a short period, significantly reducing production time.
2. Enhanced Quality
Due to its high level of accuracy, micro precision injection molding ensures that every component produced meets stringent quality standards. This reliability is particularly crucial in sectors such as medical and aerospace, where any defect could lead to significant consequences.
3. Cost-Effectiveness
While the initial costs of setting up micro precision injection molding systems may be higher, the long-term savings are undeniable. The ability to produce intricate components at scale reduces overall production costs and minimizes the need for post-processing, which can be expensive and time-consuming.
4. Greater Design Freedom
This molding method allows engineers and designers to explore innovative designs that were previously unfeasible. The ability to incorporate fine details and complex features without compromising the structural integrity of the part allows for greater creativity in product development.
Applications of Micro Precision Injection Molding
Numerous industries are leveraging the advantages offered by micro precision injection molding. Here are some notable applications:
1. Medical Devices
In the medical field, the production of surgical instruments, diagnostic devices, and implantable devices requires high precision. Micro injection molding enables the manufacturing of parts that are not only minute but can also support complex functionalities like fluid control and drug delivery.
2. Electronics
As electronic devices continue to shrink in size, the components must become increasingly precise. Micro precision injection molding is crucial in the production of housings, connectors, and other intricate parts that support modern electronics.
3. Automotive Industry
The automotive sector benefits from lightweight components produced via micro injection molding, which enhance fuel efficiency and overall performance. Parts such as sensors, connectors, and other electronic components can be manufactured with high precision, improving reliability and safety.
4. Consumer Goods
From intricate packaging designs to small mechanical components, consumer goods companies are tapping into the capabilities of micro precision injection molding to enhance the functionality and appeal of their products.
The Process of Micro Precision Injection Molding
The process of micro precision injection molding involves several key stages:
1. Design and Prototyping
The journey begins with the design of the part. Utilizing CAD software, engineers create detailed 3D models that outline every dimension and feature required in the final product. Rapid prototyping techniques can be employed to create early models for testing and validation.
2. Mold Creation
Next, precision molds are manufactured, often using advanced techniques like Electrical Discharge Machining (EDM) or Laser Machining. These molds must meet rigorous tolerance specifications to ensure that the final product will achieve the desired quality and performance.
3. Injection Process
Once the mold is prepared, the chosen material is heated until it becomes fluid and then injected into the mold cavity under high pressure. The fluidity of the material allows it to fill every nook and cranny of the mold, capturing all intricate details.
4. Cooling and Ejection
After the injection process, the material cools and solidifies, taking the shape of the mold. The manufacturing cycle continues as the molded part is ejected, and the mold is prepared for the next injection.
Challenges and Solutions in Micro Precision Injection Molding
Despite its numerous advantages, micro precision injection molding does present some challenges:
1. Material Selection
The choice of material is critical, as it affects the final part's properties. Engineers need to carefully consider factors like thermal stability, flow characteristics, and compatibility with the molding process.
2. Precision Control
Maintaining precision requires stringent control over the entire process. Advanced monitoring systems are essential to ensure that temperature, pressure, and timing are optimized, thus preventing defects.
3. Cost of Equipment
The equipment needed for micro precision injection molding can be quite expensive. However, the long-term savings and production benefits often justify this initial investment, especially for high-volume production runs.
The Future of Micro Precision Injection Molding
As technology continues to advance, the potential for micro precision injection molding is immense. Innovations such as 3D printing and smart manufacturing are beginning to intersect with traditional molding methods, leading to hybrid processes that combine the best of both worlds. Additionally, the push for sustainability in manufacturing is steering research towards less wasteful processes and the use of eco-friendly materials.
Why Choose DeepMould for Micro Precision Injection Molding
If you are looking for a reliable partner in micro precision injection molding, look no further than DeepMould. Our extensive experience as metal fabricators positions us uniquely within the market, ensuring that every project is handled with expertise and care. Here’s why we stand out:
- State-of-the-Art Equipment: We utilize the latest technology to ensure maximum precision and efficiency.
- Custom Solutions: Our team works closely with clients to tailor solutions that meet specific requirements, helping bring their visions to life.
- Exceptional Quality Control: Implementing strict quality assurance measures guarantees that every part meets or exceeds industry standards.
- Timely Delivery: We understand the importance of deadlines, and our streamlined processes ensure that your projects are completed on schedule.
Conclusion
In conclusion, micro precision injection molding is an indispensable technology that offers remarkable benefits across a variety of industries. Its ability to produce complex, high-quality components quickly and efficiently is setting new standards in manufacturing. Companies like DeepMould are at the forefront of this revolution, helping businesses harness the power of precision molding to achieve their production goals. As we move into the future, the ongoing advancements in this field promise to keep driving innovation and efficiency in manufacturing, making it an exciting area to watch.