Understanding Die Casting Mould Parts: An In-Depth Look
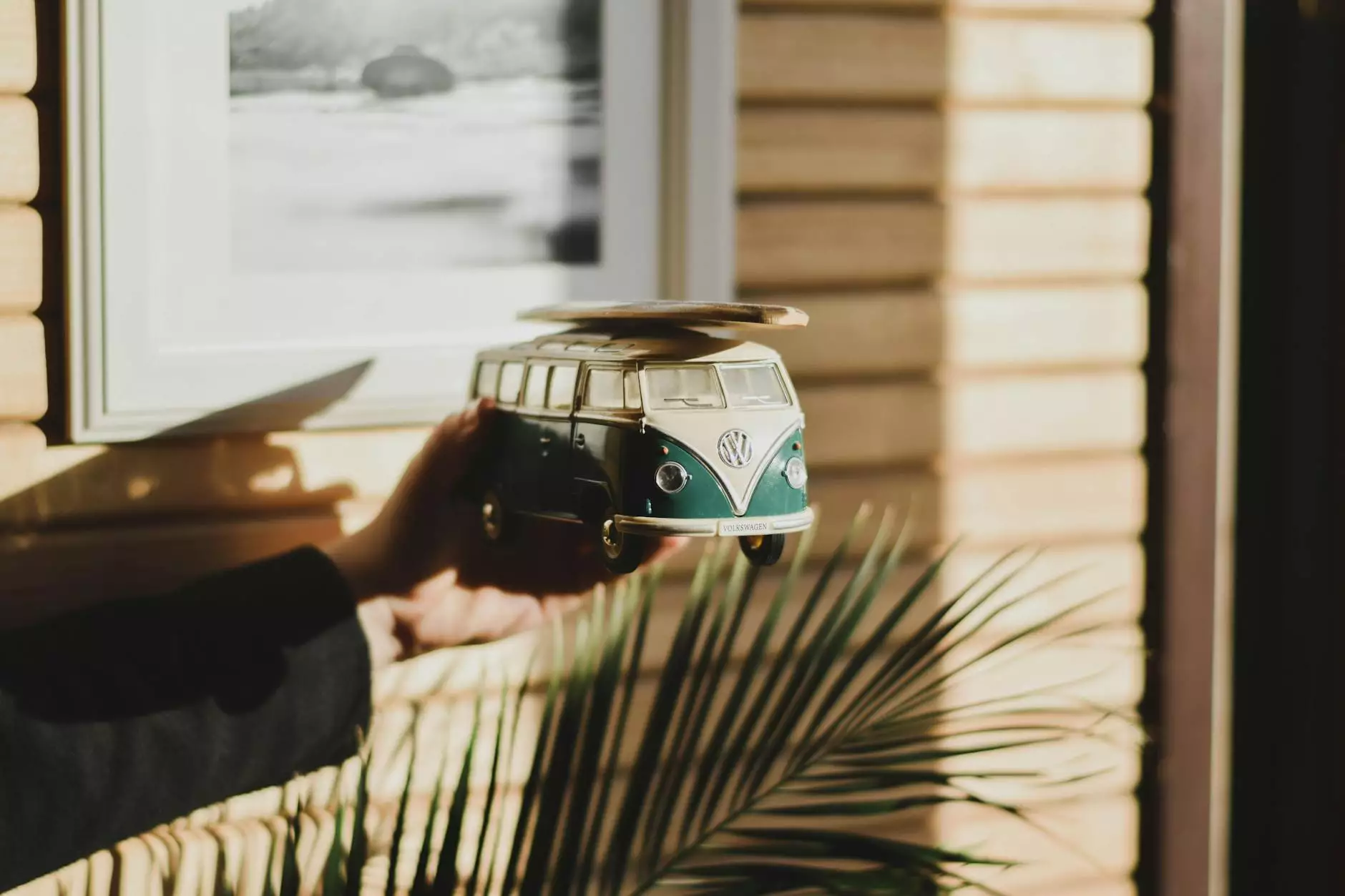
In the world of manufacturing, die casting mould parts play a critical role in producing high-quality metal components efficiently and cost-effectively. This article delves deep into the significance, processes, and benefits of die casting mould parts, particularly for businesses looking to enhance their production capabilities.
What Are Die Casting Mould Parts?
Die casting mould parts are intricate components used in the die casting process, which involves forcing molten metal into a mold cavity under high pressure. This method is prevalent for creating parts with complex shapes and tight tolerances. The mould parts themselves are designed to withstand high temperatures and pressures, ensuring durability and precision in manufacturing.
The Die Casting Process Explained
Understanding how die casting mould parts work requires familiarity with the die casting process itself. The process typically involves the following steps:
- Melt Preparation: Metal alloys (commonly aluminum, zinc, or magnesium) are heated in a furnace until they reach a molten state.
- Injection: The molten metal is injected into a prepared die (the mold) at high pressures, which helps eliminate air pockets and ensures a complete fill.
- Cooling: The molten metal cools and solidifies inside the die, taking on its final shape.
- Ejection: Once cooled, the die is opened, and the finished part is ejected.
- Finishing: Post-production processes such as trimming, machining, and surface finishing may be required to achieve the desired specifications.
Applications of Die Casting Mould Parts
Die casting mould parts are utilized across various industries due to their versatility and reliability. Some key applications include:
- Automotive: Used for producing parts like engine components, chassis, and transmission housings.
- Aerospace: Critical for manufacturing lightweight yet strong components to reduce overall weight and improve fuel efficiency.
- Electronics: Enclosures and heat sinks are produced through this method to meet stringent quality standards.
- Consumer Products: Items such as appliances, hardware, and tools often rely on die casting for their components.
- Medical Devices: Precision parts for various medical equipment are carved out using die casting techniques to ensure safety and efficiency.
Benefits of Using Die Casting Mould Parts
There are numerous advantages to employing die casting mould parts in production, including:
- Precision and Accuracy: Die casting allows for high precision manufacturing of components, which is crucial for intricate applications.
- Cost-Effectiveness: While the initial setup might be high, the efficiency and speed of production make it cost-effective in the long run.
- Complex Geometries: Manufacturers can create complex shapes and designs that may be difficult or impossible to achieve with other methods.
- Material Efficiency: Minimal waste is generated during the die casting process, making it an environmentally friendly option.
- Durability: Parts produced are exceptionally strong and resistant to wear, which enhances their lifespan.
Choosing the Right Manufacturer for Die Casting Mould Parts
Selecting the right manufacturer for your die casting mould parts is crucial to ensure quality and efficiency. Here are some factors to consider:
1. Experience and Expertise
Choose manufacturers with extensive experience in die casting. Their expertise can significantly impact the quality of the parts produced.
2. Advanced Technology
Look for manufacturers that utilize the latest technology and equipment. Advanced machines provide better precision and efficiency.
3. Quality Assurance Practices
Quality control measures are essential. Suppliers should have rigorous testing procedures to ensure every mould part meets specifications.
4. Customer Support and Service
Good customer service can make a substantial difference when communicating requirements and addressing concerns or issues.
5. Customization Capabilities
Make sure the manufacturer can accommodate custom designs to meet your specific needs, including size, shape, and material variations.
Popular Materials for Die Casting Mould Parts
The selection of material in die casting is vital in achieving the desired characteristics of the final product. Here are some commonly used materials:
- Aluminum: Known for its lightweight and resistance to corrosion, aluminum is commonly used in automotive and aerospace applications.
- Zinc: This material offers excellent strength and is often used for smaller, intricate parts.
- Magnesium: Known for its high strength-to-weight ratio, magnesium is widely used in automotive applications where weight reduction is critical.
- Copper Alloys: Copper alloys provide excellent conductivity, making them ideal for electronic applications.
Future Trends in Die Casting
The die casting industry is evolving, with several trends poised to influence its future significantly:
1. Increased Automation
Automation in the die casting process can enhance productivity, reduce human error, and improve consistency in product quality.
2. Sustainability Focus
As businesses move towards environmentally friendly practices, the die casting industry is adopting more sustainable materials and recycling processes.
3. Advanced Materials
Research and development are focused on creating new alloys that enhance performance and reduce production costs.
4. Customization and On-Demand Manufacturing
With the rise of digital technologies, manufacturers are moving towards on-demand production, reducing waste and enhancing customization for clients.
Conclusion: The Importance of Die Casting Mould Parts
In conclusion, understanding the nuances of die casting mould parts can empower businesses to optimize their manufacturing processes. By leveraging the benefits and applications of die casting, companies can produce high-quality components efficiently, positioning themselves for success in competitive markets.
At DeepMould.net, we provide industry-leading die casting mould parts designed for precision and durability. With our state-of-the-art facilities and commitment to excellence, we are here to meet all your metal fabrication needs.